Operational efficiency unlocked: Wonder’s journey to 99.9% inventory accuracy and rapid growth with OrderGrid
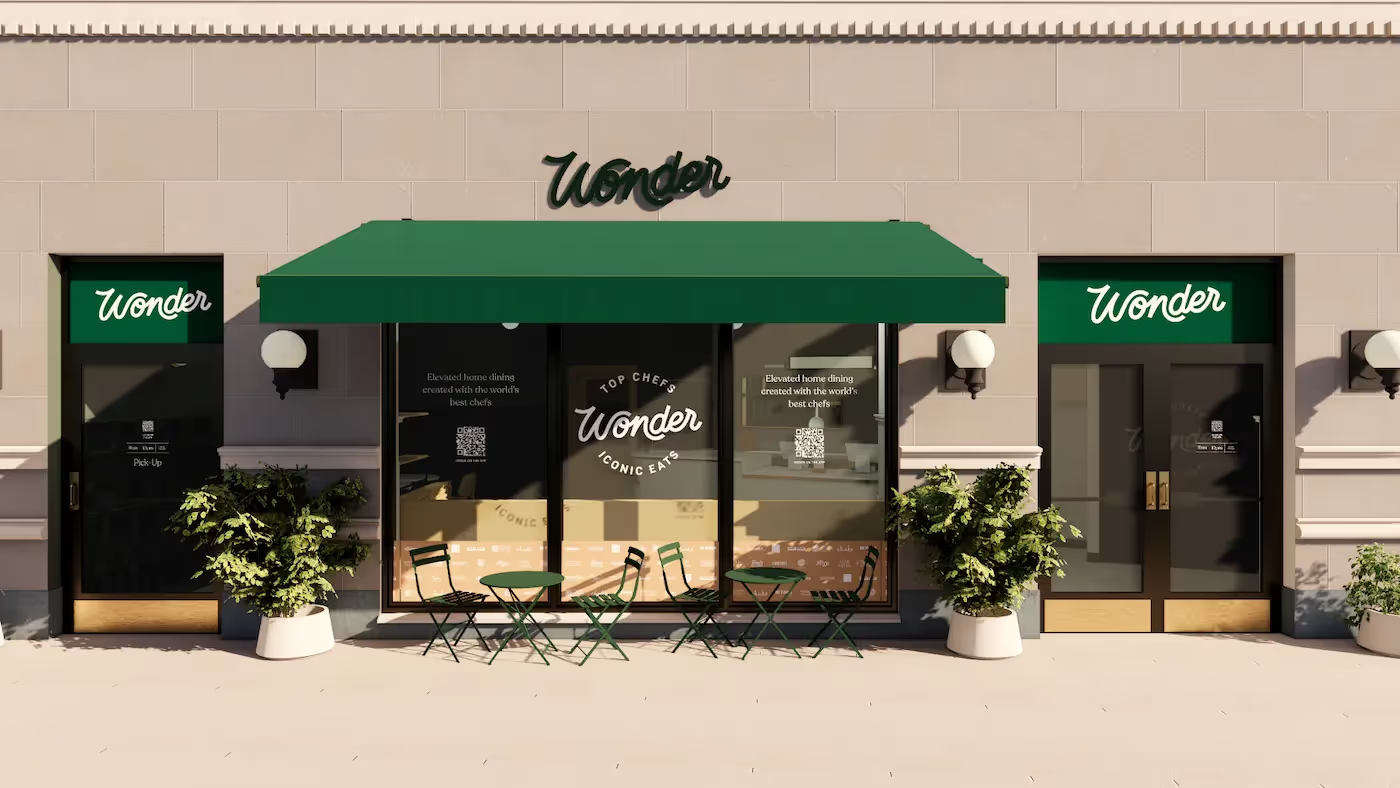
Wonder, a leading ghost kitchen and food distribution company founded by Marc Lore (former CEO of Walmart e-commerce and founder of Jet.com and Diapers.com), encountered major operational challenges during its rapid growth. Its vertically integrated supply chain, responsible for all meal pre-production, lacked the flexibility and efficiency needed for smooth operations. Relying on a rigid ERP system, Wonder struggled with inventory mismanagement, high costs, and complex distribution process. These issues resulted in waste, inflated labor expenses, and hindered growth. OrderGrid’s AI-powered inventory management system resolved these challenges, enabling Wonder to scale efficiently while cutting waste and improving accuracy.
Reduced labor costs
Inventory accuracy increased to over 99.9%
Waste reduced by over 80%
Expanded from 1 to 25 locations in 2 years
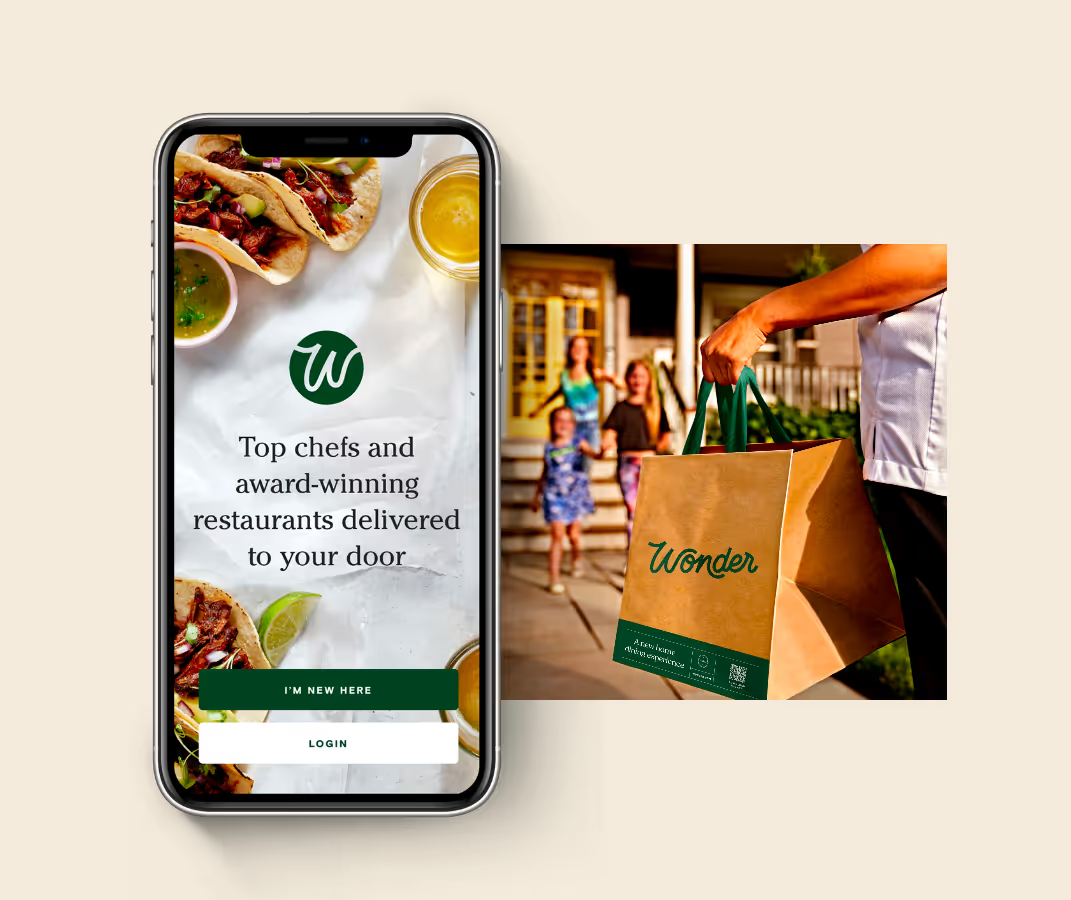
Challenge
Wonder’s operational inefficiencies increased costs and blocked growth.
Before partnering with OrderGrid, Wonder faced significant operational challenges that hindered growth. Their rigid ERP system, lacking a robust Warehouse Management System (WMS), led to several issues:
- Inventory Issues: Frequent stock shortages and excessive waste due to the lack of lot and expiration tracking.
- Inefficient Operations: Overproduction led to waste, while too many staff were required to manage inefficient workflows.
- Complex Distribution & High Costs: A complex downstream distribution process and manual purchasing inflated labor and overhead costs.
These inefficiencies drained resources and slowed Wonder’s plans for rapid expansion, making it critical to find a scalable solution to streamline fulfillment and drive growth.
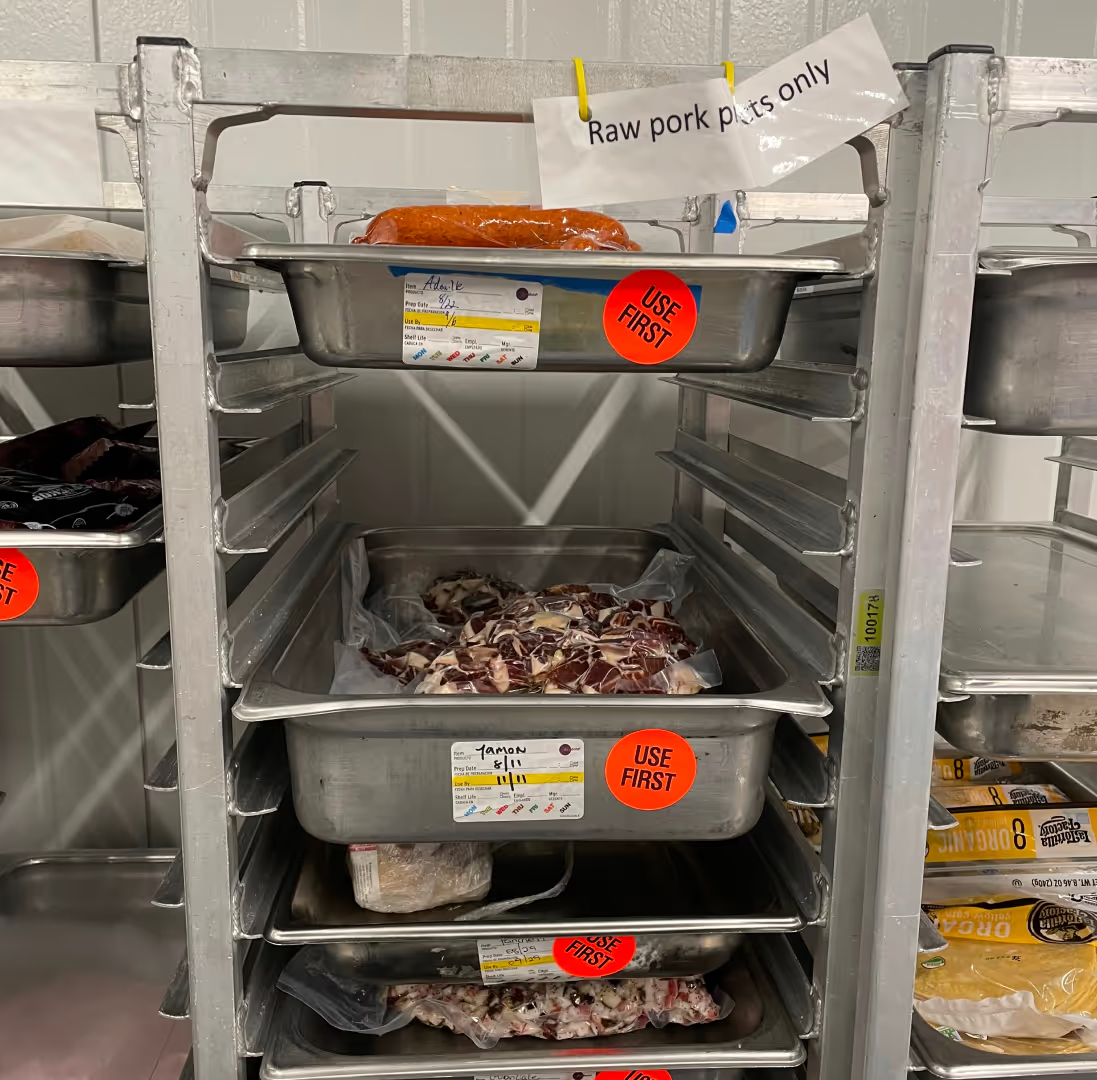
OrderGrid Solution
OrderGrid integrated with Wonder’s workflows, streamlining operations and cutting waste.
OrderGrid’s AI-powered system seamlessly integrated with Wonder’s existing ERP, optimizing warehouse operations by streamlining receiving, automating production line movements, enabling real-time inventory tracking, and simplifying distribution.
With OrderGrid’s API suite, Wonder accessed critical operational data for the first time, driving further optimization. Auto-replenishment improved accuracy, reduced waste, and empowered data-driven decision-making.
Streamlined Operations
OrderGrid’s flexible platform seamlessly integrated with Wonder’s kitchen and warehouse workflows, eliminating the need for manual workarounds. This allowed staff to work more efficiently within the system, saving time and reducing errors.
Real-time Inventory Visibility
OrderGrid’s advanced system provided Wonder with real-time, accurate data on inventory levels at every stage, from raw materials to finished products. This improved visibility enabled teams to make informed decisions, minimizing the risks of overstocking and understocking.
Scalability and Adaptability
OrderGrid’s scalable infrastructure enabled Wonder to expand without encountering operational bottlenecks. The system’s agility allowed Wonder to swiftly adapt to changes in their business model and market demands, all while maintaining efficiency.
Impact
Waste Reduction
With better forecasting and real-time insights, Wonder saw a dramatic decrease in excess inventory and associated waste, promoting both financial savings and environmental sustainability.
Operational Efficiency
The efficiency gained through optimized inventory management and delivery operations resulted in higher throughput, contributing directly to the growth in same-store sales.
Enhanced Scalability
OrderGrid’s platform empowered Wonder to scale operations seamlessly. By allocating resources more efficiently and reinvesting savings from reduced waste, Wonder was able to fuel growth, adding a new site each week.
Sustainability
In addition to cost savings, Wonder’s newfound efficiency contributed to its environmental goals by reducing overproduction and unnecessary waste. This commitment to sustainability aligned with Wonder’s vision for responsible growth.
Conclusion
OrderGrid optimized Wonder’s efficiency, reduced waste, and fueled rapid growth.
OrderGrid’s AI-driven inventory management system was instrumental in helping Wonder overcome significant operational challenges.
By providing real-time visibility, intelligent forecasting, and an flexible infrastructure, OrderGrid enabled Wonder to boost efficiency, reduce waste, and scale sustainably.
As Wonder continues to grow, OrderGrid’s platform remains a vital component of its success, supporting both financial and environmental sustainability.
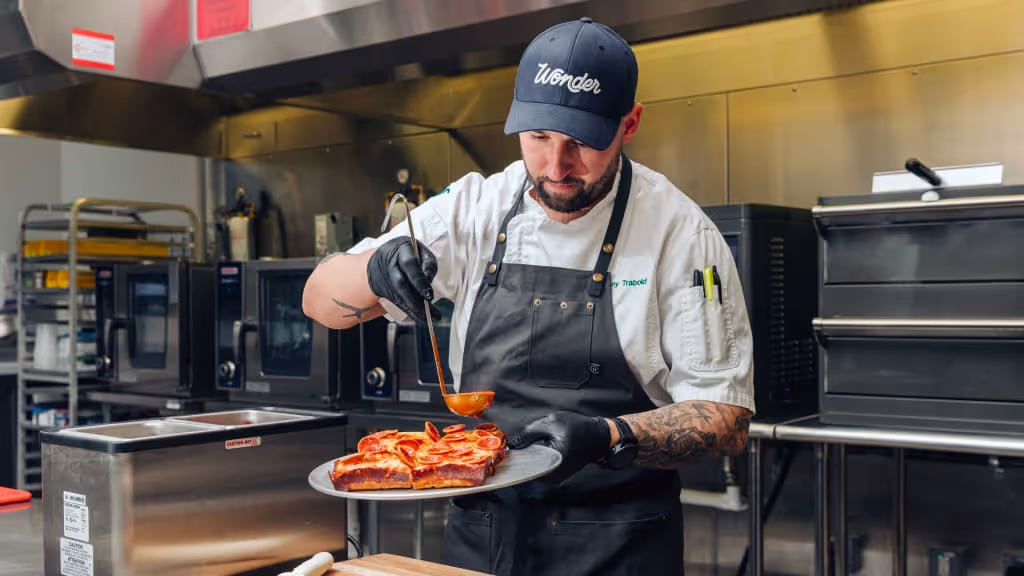
Contact us to learn more
Our experts are ready to field your questions about fulfillment, saving on costs, international scaling, and more. Reach out to learn more today.